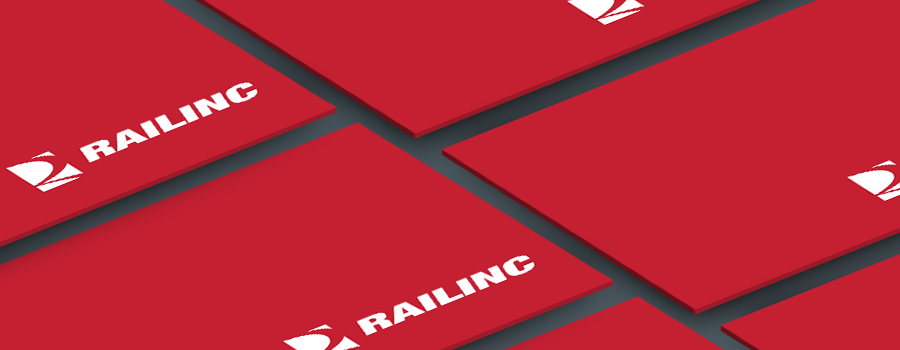
The sticky notes you find around Railinc tell stories about our culture and how we develop our products; how we learn from and work with our customers; and how we meet the technology needs of the freight rail industry. A regular feature on the Railinc Tracks blog, Found on a Sticky Note takes a look at an individual sticky note and provides insights into who we are and what we do.
The North American freight rail industry depends on rules and processes to ensure the proper movement, interchanging, monitoring and repair of more than 1.5 million railcars across the 144,000-mile North American rail network.
Why are these rules so important?
"They externalize business logic, enable business agility and enforce data quality around activities that are critical to safe and efficient rail operations," said Jerry Vaughn, Railinc's director of interline product management.
Freight rail operations are complex. Rail carriers haul and interchange cars that do not belong to them. A railcar owned by a company on the East Coast might get pulled from service for repairs on the West Coast. Railcars and individual components need regular testing and inspection, no matter where they are. Data on activities such as repairs and recalls have to be reported and shared across the industry to verify the health of railcars in service.
Industry rules help to ensure the entire industry applies the same standards to these types of tasks. Contained within the Association of American Railroads' official rules manuals, industry rules cover everything from component characteristics to data reporting procedures to processes around car hire. Many of Railinc's systems and applications are designed to support these rules-based activities and are embedded in critical operations and financial systems throughout the industry.
Two Sentences Help Reduce Customer Confusion Around a Rule
The sticky note above summarizes a user story connected with the freight rail industry's Rule 107 and was part of work completed in late 2015 on Railinc's Damaged and Defective Car Tracking (DDCT) system. The note reads:
US32251
Notification — Rule 107
Update verbiage
A centralized system for tracking damaged and defective railcars, DDCT standardizes the process for reporting and storing data on these cars. For decades, this information was documented on a 3 1/2-inch by 8-inch paper defect card affixed to the side of a railcar. Companies maintained their own tracking systems, which often led to conflicting or unavailable data and required car owners to contact carriers to find out a car's condition.
A defect card holder on the side of a railcar.
Implemented in January 2011, DDCT standardized these processes, improving data accuracy and timeliness, reducing administrative costs for railroads and car owners, and improving the enforcement of industry car hire rules. Industry rules require that rail carriers, car owners and repair shops use DDCT for all cars that participate in interchange.
![]() |
Railinc team members at the whiteboard. |
Rule 107, referenced in the sticky note, establishes the sequence of events that must occur to compensate a railcar owner whose equipment is damaged or destroyed. For example, if a railcar is damaged during interchange, the responsible rail carrier must follow steps detailed in Rule 107 to reimburse the car owner for the damage or to pay for the repair.
DDCT sends auto-generated email notifications to car owners throughout this process, helping them stay informed about the status of their cars.
"Based on what we were hearing from our customers, one of our emails needed more information," said Sophie Hamida, a business analyst on the DDCT team. "Car owners were taking time to call Railinc to find out why the system was displaying the data it was."
In this case, the repairs on a railcar might be complete, but the incident did not show in the system as being closed and the car itself was not removed from the related maintenance advisory. The DDCT team added verbiage to the email that detailed the timeline for closing the Rule 107 incident.
"The aim was to reduce customer confusion about why a car that might have returned to service still showed up in the DDCT system as an open incident," Hamida said. "We only added two sentences to the email, but it will help make what can be a challenging process a little easier for customers."
Railinc Program to Modernize Rules Management
The business logic, rules and processes embedded in Railinc products help to enable the enforcement of industry requirements, like Rule 107. Last year, the company launched a multi-year Rules and Process Modernization (RPM) program, which will modernize the management of the industry rules and processes that underlie our applications and systems.
The RPM program leverages technology to enable the company to take a more consultative approach with customers and helps to improve the efficiency, consistency and reliability of these rules and processes within Railinc applications. DDCT was among the program's proof of technology projects.
"Nearly half of our project development activities involve the implementation of business rules and processes," said Jeanine Bradley, senior manager for business rules and process management.
These rules and processes have traditionally been buried in code in Railinc applications. Because they were not visible and documented with a common language, it has been challenging to respond quickly to customer questions or requests for changes to applications.
"The RPM program is an effort to advance how we manage rules and processes within our applications," Bradley said. "We want to be able to eliminate the complexity so we can support our customers better and deliver innovative solutions that meet the ever-changing needs of the industry."
—Railinc Corporate Communications