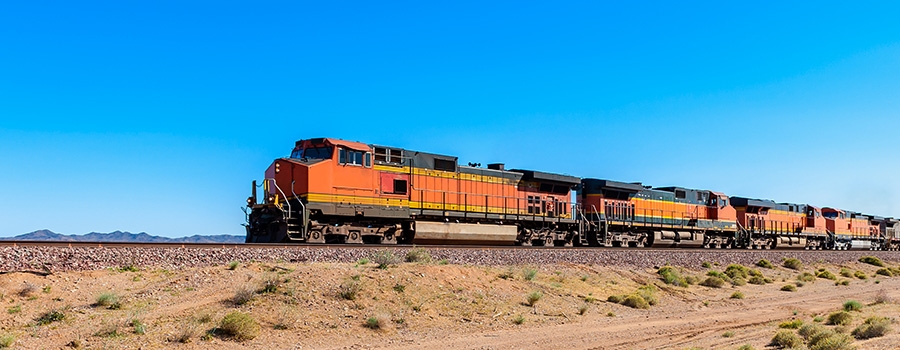
Railroads that follow the AAR rules of interchange for inspections and repair bill for most maintenance using the AAR price master. For some smaller roads, that may mean paying more in costs to complete repairs than what can be billed to the car owner.
Since repairs priced at AAR rates are set by the industry, the only costs under a shop's control are overhead charges. Reducing your overhead costs allows the reduction to cover a portion of the actual repair costs, increasing the overall margin for car repairs.
So how can a railroad reduce their overall cost of maintenance?
Automate Time-Consuming Billing Tasks so Your Mechanics Can Get Back to Repairing Cars
Preparing for Inbound Inspection
When preparing for the inspection, many railroads currently note the inbound cars’ alerts and other health information on paper or in a spreadsheet, searching and recording data from both Equipment Health View and Umler®. While the information gathered from these systems provides the needed car health and alert information, multi-system searching is time-consuming and inefficient. Gathering car information can cost your team between 30-60 minutes for each 200-car train. If equipment health information is quickly accessible, your shop can understand which cars need to be bad ordered and what kind of repairs to be prepared for, faster.
Shop Switching
Equipment held for parts can increase demurrage fees, making shop efficiency vital. Having to kick out a car that remains bad ordered for days creates unnecessary work for the transportation team to re-sort a bad-ordered car. If your business regularly sees hold for inventory events, your shop is likely not identifying the type of materials needed before the car arrives for repair. A Car Health and Umler-integrated billing system can provide actionable knowledge to reduce time and money spent on shop switching.
Recording Repairs
Accurate repair recording is essential for accounting and quality assurance, but the process shouldn’t be painful for your shop. The opportunity cost of having your most senior mechanical member tied up with billing issues could be time lost in training, incorrect handling of the actual repair or overlooked damages. Or, your team could have to wait for the shop foreman to look at a repair, increasing dwell time and slowing shop operations. Car repair software that aids in accurate, easy repair entry can help. Our CarLogix solution provides job code lookup and up-to-date industry rules, saving your team time.
Maximize Revenue
Missed Billing
Missed billing costs some businesses thousands of dollars before it’s recognized as a problem. Identifying missed billing would require your team to check bills as they are created and remember every possible situation of associated billing. Again, human error is inevitable. Even if your team manually reviews billing before invoicing, which is incredibly time-consuming, you are still likely to miss exception opportunities. That doesn’t have to be the case. A smart repair management software will identify associated repairs that are recommended or required, suggest them to you, and ensure they are entered.
Double Billing
Double billing is also difficult to catch, and net applied repairs are often the culprit. If you bill twice for nuts and bolts that a previous job code entry covered, you’re likely to receive an exception to manage. If your shop is seeing these exceptions, you’re missing a CRB that checks for duplicates.
Summary
If your shop still deals with exceptions or spends a significant amount of time on billing, it’s time to consider switching software providers. Here’s a checklist of ways our CarLogix system can help drive shop efficiency:
- Integrating Car Health and Umler alert information: This allows you to know what damage exists on a car before cars arrive.
- Text lookup for job codes: This reduces the amount of memorization and specialized knowledge needed to bill. Using text lookup means the person entering the repair doesn’t necessarily need to memorize every job code.
- Rule-based entry: Entries that align with the most up-to-date AAR rules help guarantee that your shop won’t have to spend time managing exceptions later. Ensure your provider updates AAR rules at the same time as they go into effect.
- Real-time validation: Human errors are unavoidable. A system should immediately let you know that there’s an error and allow you to correct it on the front end, rather than through the time-consuming and costly exception process.
- A provider that understands AAR processes: Validating entries against outdated rules doesn’t help your shop. Ensure AAR rules are immediately updated as they change. To do this, your provider needs to have specialized industry knowledge, not just an understanding of technology.
An efficient repair process may take effort to implement but is essential to reduce costs. Does your system do all of the above? If not, it’s time to consider switching. We designed our next-generation asset management software, CarLogix, with all of the above efficiency-driving features.
The requirements of car repair billing are constantly changing, so keep up with ways to optimize your business by visiting the Railinc Tracks blog regularly or connecting with us on social media.
This blog was contributed by the Railinc CarLogix team, which has more than 20 years of car repair billing experience. Learn about CarLogix here.