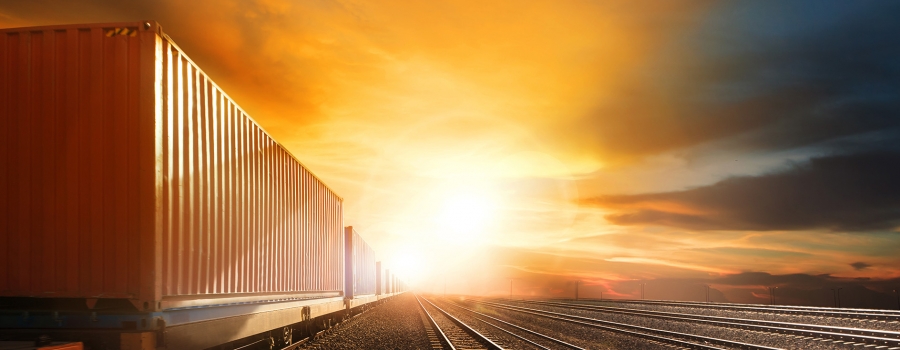
Rail cars must function safely and efficiently whatever the environment sends their way—fully loaded or empty; at the front, rear, or middle of a freight train; in extreme operating conditions; and across difficult geographical terrains.
There is an ever-increasing focus on asset health management leading to new solutions that improve safety and efficiency. With more and better data around asset health, failures can be reduced and the reliability of rail car operations can be improved.
This is being accomplished with more sophisticated wayside detection systems, tracking of critical railcar components, better operating practices, machine learning and automated intelligence.
This new way of looking at railcar reliability is making rail operations more fluid. Traditionally, if a train stops due to an equipment malfunction the conductor is obligated to walk the train in search of the problem, whether it’s raining, snowing, blazing hot or bitterly cold. Sometimes, out there in the elements the cause remains elusive.
Meanwhile, the main line is tied up. Traffic on either side of the stopped train comes to a halt. Sometimes, the chain reaction can extend far beyond a specific location. Costs quickly pile up. There are multiple impacts to a single event like this.
Fortunately, this scenario is increasingly being relegated to the past.
Faster, smarter networks of detectors help avoid these situations. Using data collected throughout North America, mechanical problems are identified before or as they develop, allowing ample time to take proactive measures that prevent those problems from causing track damage or train delays.
We now have data flowing from a number of wayside detectors and train events including:
• Wheel Impact Load Detectors
• Truck Hunting Detectors
• Acoustic Bearing Detectors
• Truck Performance Detectors
• AEI Detectors
• Line of Road Mechanical delays
These systems allow the industry to collect massive amounts of data on such components as wheels, axles, bearings and brakes. New advanced analytical algorithms make it possible to track cars that have proven to be culprits in multiple events—they’ll rise to the top of the list so they can be quickly taken out of service and fixed.
The benefits of improved asset health management are significant because all the players are working together. It is estimated that that one of the network improvements has been the prevention of as many as 5,200 car failures per year, translating to about $5 million in annual savings. That’s an important victory for both railroads and their shipping customers.